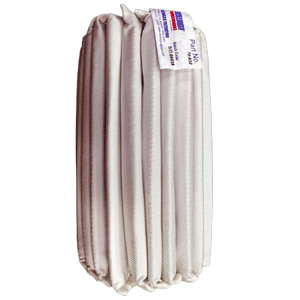
Eriez’ Drum Separators are setting industry standards. The newest advances in magnetic circuitry design, plus over a quarter of a century of experience with solid/liquid separation, are combined in Eriez Wet Magnetic Drum Separators.
Innovations in both magnetic circuit design and materials of construction are applied to Eriez wet drum magnetic separators. This results in maximum magnetite recovery while operating with a minimum amount of wear and maintenance. Refinements in the magnetic circuit, tank design, and drive system have resulted in further improvements in metallurgical performance and operation.
Features & Benefits:
Wet Drums for Heavy Media Duty
Wet drums in heavy media applications provide continuous recovery of magnetite or ferrosilicon. Eriez has set the industry standards in the heavy media industry developing both the design criteria of the magnetic circuit and the benchmark of operation. The 750 gauss Interpole magnetic element, developed by Eriez, is the most acclaimed magnet of engineering standards in the industry. Eriez has also set the benchmark for wet drum performance. The culmination of various in–plant tests has demonstrated that the separators will achieve magnetite recoveries in the 99.9+ percent. (This is based on magnetite losses of less than 1 gram/gallon of non–magnetic effluent).
Eriez offers two styles of tanks. The drum rotates in the same direction as the slurry flow in the concurrent tank style. The counter-rotation tank style is preferred for heavy media applications.
Wet Drums for Concentration Duty
Wet drum magnetic separators are the most vital part of the upgrading process in magnetite concentration. The upgrading of primary magnetite is always accomplished with wet drum separators. Mill feed is typically upgraded to 65+ percent magnetic iron using a series of wet drum magnetic separators. The number of magnetic separation stages required to upgrade the ore is dependent on the magnetite content and the liberation characteristics of the ore.
The Eriez Wet Drum Magnetic Separators is engineered and fabricated to provide reliable operation in demanding applications. The separator is designed for the continuous treatment of coarse milled ore providing a high level of availability. The tank and drum are fabricated from heavy gauge stainless steel with wear plate in impact areas. Wear areas are protected with hot vulcanized rubber. The drum utilizes heavy–duty spherical roller bearings with a B–10 life of 100,000+ hours. The drive system utilizes a Mill and Chemical Duty motor coupled to a shaft mounted gear reducer complete with Taconite Seals.
The feed enters the separator at the bottom of the tank and the drum rotates in the same direction as the slurry flow. This tank also has a scavenging zone. The nonmagnetics must migrate through the magnetic field to a full width overflow. This design, with the full width overflow, allows the tank to be self–leveling. There are no tailings spigots that must be adjusted to match the flow of the separator feed. This design is most effective for producing a clean magnetite concentrate. The magnetic element should incorporate several agitating magnetic poles to provide a high degree of cleaning. Since the finisher feed consists of fairly well liberated magnetite, extreme magnetic field strengths are not required for collection.
Since 1976, we’ve helped manufacturers with their filtration, process & material handling needs. From filtering air, gas & liquids to moving, processing & packaging bulk solids – we’ve successfully done it.
Join our newsletter for updates and tips to improve your industrial process.