The Metalfab Bin Activator is a rugged and proven bin activator and has provided dependable flow inducement for over 50 years. The tendency of dry solids to flow from bins in a sporadic or irregular fashion has perplexed the materials handling industry from its earliest days. Attempts to solve the problem have ranged widely – and wildly – from the use of a laborer with a sledge hammer, to rappers or vibrators and powerful blasts of air. Over the years no single method or combination of techniques ever provided a universally successful solution. Then in 1960, a revolutionary new concept was introduced which overcame the troublesome and costly problems of arching, bridging, and rat-holing. Called a “Bin Activator”, the device consisted of a vibrated cone which was suspended beneath the bin, replacing a major portion of the standard fixed cone. Positive discharge was achieved through the successful application of the principles of vibration as well as by the design of the unit.
Today, the most effective bin activator designs incorporate the use of an internal cone-shaped baffle which is rigidly attached to the body of the bin activator by means of rugged structural tubular members. The entire bin activator unit moves horizontally in response to centrifugal forces generated by the unbalanced weights of an attached vibrator.
Metalfab Bin Activator – Dual Baffle
Material flows smoothly around the primary baffle and when it narrows down and squeezes its way toward the outlet, the secondary baffle prevents it from compacting and jamming. Flow through the outlet is constant and upon demand. No need for cycling.. no need for excessively large outlets.
The cone baffle relieves the weight of the material from the lower section of the bin activator, and acts like a wedge as it moves beneath the material and pushes it in all areas adjacent to the cone’s surfaces. This powerful force is also transmitted to the material in the upper portion of the bin as the motion is carried from particle to particle.
These moving particles cannot bridge or rat-hole, and flow freely around the periphery of the baffle toward the outlet of the bin activator. If the outlet is large enough and there is no downstream equipment to impede the flow, positive discharge is accomplished.
However, where flow is regulated by other devices, the material may become jammed or compacted at the outlet, causing a no-flow condition. The shape of the unit is irrelevant; it makes no difference whether it is dish-shaped, cone-shaped or multi-sloped. For as long as the material must travel from a larger dimension to a much smaller one at the discharge hole, convergence must take place. Vigorous vibration only serves to worsen the problem. To solve the problem, Metalfab introduced its secondary baffle design. The secondary baffle prevents jamming and compaction of the material at the outlet and allows for a constant flow upon demand.
Sanitary constructed units with 3A dairy approval, are available in all sizes.
Features/Benefits
- Wide Range of Sizes: 2′ to 16′ diameter
- Unique Dual Baffle Design: features a primary and suspended secondary baffle that delivers continuous flow of dry materials without plugging, jamming or bridging
- Endless beaded Flexible Sleeve: is 7/16″ thick with 3-ply reinforcement that will not puncture, slip or leak
- Solid Steel Suspension Arms: are bolted 90º and can support up to 5000,000 lbs. each to ensure the bin activator will always remain attached to the bin and cannot move off-center
- Unitized Vibrator and Motor: combines the vibrator and motor in a single, sealed enclosure with no belts to slip or break – unconditionally guaranteed for 30 months
- Performance Guarantee: every Metalfab bin activator is guaranteed to perform in accordance with specifications or the purchase price will be refunded
Operating Characteristics
- Delivers long-lasting performance with low maintenance, maximum process “uptime” and high standard quality – all at a very competitive price
- Features an exclusive dual baffle to prevent compaction of material
- Construction Materials: Carbon steel, special coatings, 304SS, 316SS
Construction
- Carbon steel, special coatings, 304 or 316 stainless steel
Available Options
- Maintenance slide gate
- Explosion proof
- Positive or negative pressures
- Other Metalfab upstream/downstream bin activators, Covey-All™ Conveyors, bulk bag unloaders, Posibins™ and hoppers
Model | DIA | O.D. | I.D. | A | B | C | D | No. of Hangers | TENV HP |
---|---|---|---|---|---|---|---|---|---|
BA-2 | 2′ | 26 1/2 | 23 1/2 | 16 1/2 | 22 | 2 1/4 | 15 3/4 | 4 | 1/2 |
BA-3 | 3′ | 41 3/8 | 35 3/8 | 22 5/8 | 31 3/8 | 2 3/4 | 16 1/4 | 3 | 1 1/2 |
BA-4 | 4′ | 53 1/4 | 47 1/4 | 29 1/2 | 35 1/4 | 4 1/8 | 22 7/8 | 4 | 1 1/2 |
BA-5 | 5′ | 65 1/4 | 59 1/4 | 36 3/16 | 41 1/4 | 4 1/8 | 22 7/8 | 4 | 1 1/2 |
BA-6 | 6′ | 79 1/4 | 71 1/4 | 43 1/8 | 49 1/16 | 3 11/16 | 27 13/16 | 6 | 3 |
BA-7 | 7′ | 91 1/4 | 83 1/4 | 50 | 55 1/4 | 5 1/8 | 26 3/8 | 6 | 3 |
BA-8 | 8′ | 103 | 95 | 56 7/8 | 61 1/2 | 7 7/8 | 29 1/8 | 8 | 3 |
BA-10 | 10′ | 127 | 119 | 70 | 77 11/16 | 10 7/8 | 34 1/16 | 16 | 4 |
BA-12 | 12′ | 151 | 143 | 81 | 92 1/4 | 11 1/8 | 44 | 20 | 6 |
BA-14 | 14′ | 175 | 167 | 85 | 107 | 14 | 47 | 20 | 10 |
BA-16 | 16′ | 199 | 191 | 103 | 118 | 14 | 47 | 24 | 10 |
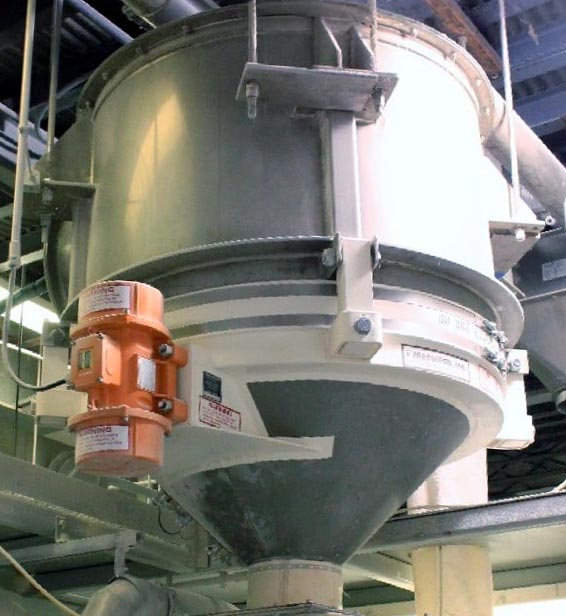