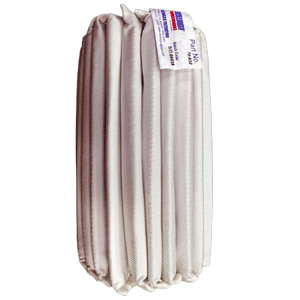
Dollinger StayNew® Spin Filter Systems are designed to beat tough contaminants like fly ash, soot, dust, sand, grit, saw-dust, rain and snow and operate continuously. They provide clean, smooth air flow in a wide variety of hostile environments and conditions – even sandstorms and volcanic fallout.
All smooth-flow compressor and blower installations can benefit from the performance and economy of a multi-stage StayNew® Spin Filter System. Their self-cleaning feature makes these systems ideal for locations where heavy contaminant loading is a problem for air intake filtration. Their strong corrosion-resistant construction means you can install them in locations where conventional filters are not suitable.
Dollinger has designed these systems to help you cut costs with pre-engineered, modular units to fit most applications. We can also custom design units with a large selection of accessories and options.
Examples of installations include:
StayNew® Spin Filter Module
The Dollinger StayNew® Spin Module, which is the heart of the StayNew® Spin Filter System, is a compact mechanical separator which can be used independently or in combination with secondary filter elements in a variety of air filtration systems. It is designed to conquer tough contaminants, providing clean, smooth air flow in a range of applications and conditions.
The self-cleaning feature makes it ideal for locations where heavy contaminant loading is a problem for conventional air-intake filtration. The strong corrosion resistant construction means the StayNew® Spin Filter Module can be installed in hostile environments. In addition, it is unaffected by wide ambient temperature variations – maintaining stability and operational integrity from – 40°F to + 200°F. The StayNew® Spin Filter Module is also safe for food service and has received FDA clearance for food contact use (21 CFR 177.1520).
By greatly reducing dirt loading on secondary filter elements in a system, the StayNew® Spin Filter Module provides long-term economies by extending the service life of an air-intake system. Used alone, it removes 98% of solid particles 15 microns and larger from an air stream. In addition, it will remove up to 99.4% of moisture, whether in the form of liquid mist or snow.
The standard StayNew® Spin Filter Module, VE-616-1220, is a twin module. Nominally rated at 1,450 SCFM, it can successfully accommodate flow rates up to 2,800 SCFM. The compact, lightweight, modular construction of the unit allows for multiples to be combined readily in a package to handle the most demanding requirements. Also available for special applications is a single module, VE-616-1210, The rated capacity of the smaller units is 725 SCFM.
Design and Construction
The standard StayNew® Spin Filter Module is mold-formed of rugged, high-density polypropylene. Through centrifugal force, contaminants are removed from the air stream as it is drawn through tubes. The StayNew® Spin Filter Module’s remarkable efficiency is the culmination of years of engineering design, laboratory developments and field testing.
Efficient Operation
Air enters inlet tube, striking stationary spinner and developing high radial velocity. Inertial action forces contaminants to the periphery of the tube, separating them from the main air stream. Main air stream, now cleaned, exits straight through the center discharge tube. Contaminants are carried by a secondary discharge stream into a bleed duct system. A blower is used to provide suction for the bleed air (approx. 10% of the inlet flow).
Since 1976, we’ve helped manufacturers with their filtration, process & material handling needs. From filtering air, gas & liquids to moving, processing & packaging bulk solids – we’ve successfully done it.
Join our newsletter for updates and tips to improve your industrial process.